Warehouse management has come a long way from manual processes and paperwork. Today, technology is at the heart of efficient operations, with many innovative tools redefining how things are done. Businesses that embrace these changes often see a dramatic boost in productivity and accuracy. But, navigating this high-tech landscape can be daunting without knowing where to start.
In this article, we delve into some of the exciting technologies transforming warehouse management. Whether you're looking to improve inventory accuracy, speed up order processing, or optimize storage, understanding these innovations could be the key to unlocking significant advantages. From the role of automation and robotics to the power of AI and IoT, there is a wide range of solutions ready to be explored. Stick around, and let's embark on a journey to discover how these technologies are reshaping the industry.
- Introduction to Modern Warehouse Technology
- The Role of Automation in Warehousing
- Artificial Intelligence and Machine Learning
- The Internet of Things (IoT) in Inventory Management
- Robotics Enhancing Storage and Retrieval
- Future Trends and Innovations
Introduction to Modern Warehouse Technology
In the bustling realm of warehouse management, innovative technology serves as the cornerstone of revolutionizing systems across the globe. This transformation stretches beyond mere machinery, capturing advancements that blend seamlessly with human processes, magnifying both efficiency and precision. Intrinsically linked to the supply chain, these technologies foster environments where productivity flourishes and operational setbacks are minimized.
Among the trailblazers in this arena are the awe-inspiring automation systems, which have become more sophisticated each year. These mechanisms undertake monotonous or even strenuous tasks, allowing human counterparts to focus on higher-level strategic operations. For instance, conveyor belts, once seen as state-of-the-art in their own right, now collaborate with integrated sensors and software to form intricate automated workflows. An interesting facet is that the International Data Corporation (IDC) reported that companies that have adopted such solutions witnessed improvements of up to 25% in order-processing speed. Such statistics shed light on the undeniable impact these technologies wield.
But the spotlight isn’t fixed solely on machinery. Cutting-edge software applications enhance real-time inventory tracking, significantly reducing wastage and misplacement risks. Imagine being able to pinpoint the exact location of an item in a massive warehouse without lifting a finger. A well-tailored Warehouse Management System (WMS) makes this possible, offering instantaneous insights that aid in decision-making processes. These systems often marry well with other digital infrastructures, such as Enterprise Resource Planning (ERP) tools, aligning efforts across the entire business landscape. A notable observation from Forbes highlights that companies wielding integrated systems report a 30% rise in inventory accuracy, underlining the effectiveness of these innovations.
Meanwhile, endeavors in Artificial Intelligence (AI) push boundaries even further, introducing capabilities that parallel human intuition in some respects. AI systems analyze myriad data points, unearthing patterns and inefficiencies which may elude the human eye. In fact, using AI, businesses can predict trends and demands with a remarkable degree of accuracy, transforming how inventory is managed seasonally and during fluctuating market conditions.
As stated by John Smith, a logistics expert with over 15 years in the field, "The integration of AI in warehousing is akin to having an expert analyst working 24/7, tirelessly improving operations and preemptively solving issues." This sentiment echoes through an industry poised on the brink of an technology-driven reshaping.
Understanding the impact of these technological breakthroughs requires a robust examination of statistics and tangible case studies, which consistently demonstrate their benefits. For example, a recent study by logistics specialists suggested that investment in such technology could yield a return on investment upwards of 50% within three years, a reassuring figure for stakeholders contemplating the leap into modernization.
Observed trends signify that the wave of technological adoption is not merely transient. It represents a shift towards an age where warehouses operate like smart cities—nodes of information seamlessly connected and perpetually adapting. By integrating state-of-the-art technology into the daily rhythm of warehouse management, companies not only streamline operations but also create a more sustainable future. This philosophy is shaping how we perceive the roles technology can inhabit within the storied processes of warehousing.
The Role of Automation in Warehousing
Automation in warehousing is changing how businesses operate, offering remarkable efficiencies in managing inventories and fulfilling orders. It involves using technology to perform tasks that once required humans, ranging from the simple to the complex. Automated systems are capable of handling repetitive tasks with precision, ensuring a level of consistency that's difficult to achieve manually. By integrating automation into warehousing, companies can significantly reduce errors in inventory management and streamline operations.
One of the standout benefits of automation is its ability to enhance speed in processing and picking operations. Automated Picking Systems (APS), for instance, use conveyors, barcode scanners, and computer systems to quickly move and identify products through the warehouse. This enhances accuracy and cuts down significantly on the time required to prepare shipments, which is crucial in today's fast-paced market dynamics where customers expect rapid delivery. According to a report by McKinsey, automation can enhance productivity in warehousing operations by up to 40%, primarily by reducing manual errors and optimizing labor usage.
Another crucial aspect of warehouse automation is in handling large data sets with agility and accuracy. These systems can seamlessly track inventory levels, reorder quantities, and generate restocking alerts. This data-driven approach ensures that the right amount of product is always on hand, reducing the risk of stockouts while avoiding overstocking, which ties up capital. Inventory management software today often integrates with automated systems to enable real-time tracking and analysis. As Fred Smith, Founder of FedEx, once emphasized,
Information about the package is sometimes as important as the package itself.This emphasizes how crucial real-time data is in modern warehouse operations.
The impact of automation on labor cannot be ignored. It is not primarily about replacing jobs but reallocating resources more effectively. While automation handles tedious tasks, employees can focus on more strategic roles such as quality control, process improvement, and customer service, thereby playing a critical role in enhancing the overall efficiency of the warehouse. Additionally, given the physical nature of warehousing, automation can also enhance safety. By employing automated systems to manage heavy lifting or potentially dangerous tasks, warehouses can significantly reduce the risk of workplace injuries.
Furthermore, automation contributes to energy efficiency in warehousing. For instance, Automated Guided Vehicles (AGVs) are engineered to optimize routes within the warehouse, leading to less energy consumption compared to traditional manual operations. Some advanced systems also employ energy-efficient motors and regenerative braking systems, which not only saves energy but also reduces operational costs. This aspect is becoming increasingly significant as more businesses strive for sustainability in their operations.
A deeper dive into warehouse automation reveals the impressive level of customization available to meet specific business needs. Whether it’s incorporating Automated Storage and Retrieval Systems (ASRS) for vertical space optimization or employing collaborative robots (cobots) for flexible support roles, the possibilities are vast. This flexibility makes automation a valuable tool for businesses of all sizes, as it can be tailored to fit specific operational demands and expand alongside the business. Automation isn't a one-size-fits-all solution, but rather a scalable approach that can grow and evolve, adapting to new challenges as they arise.
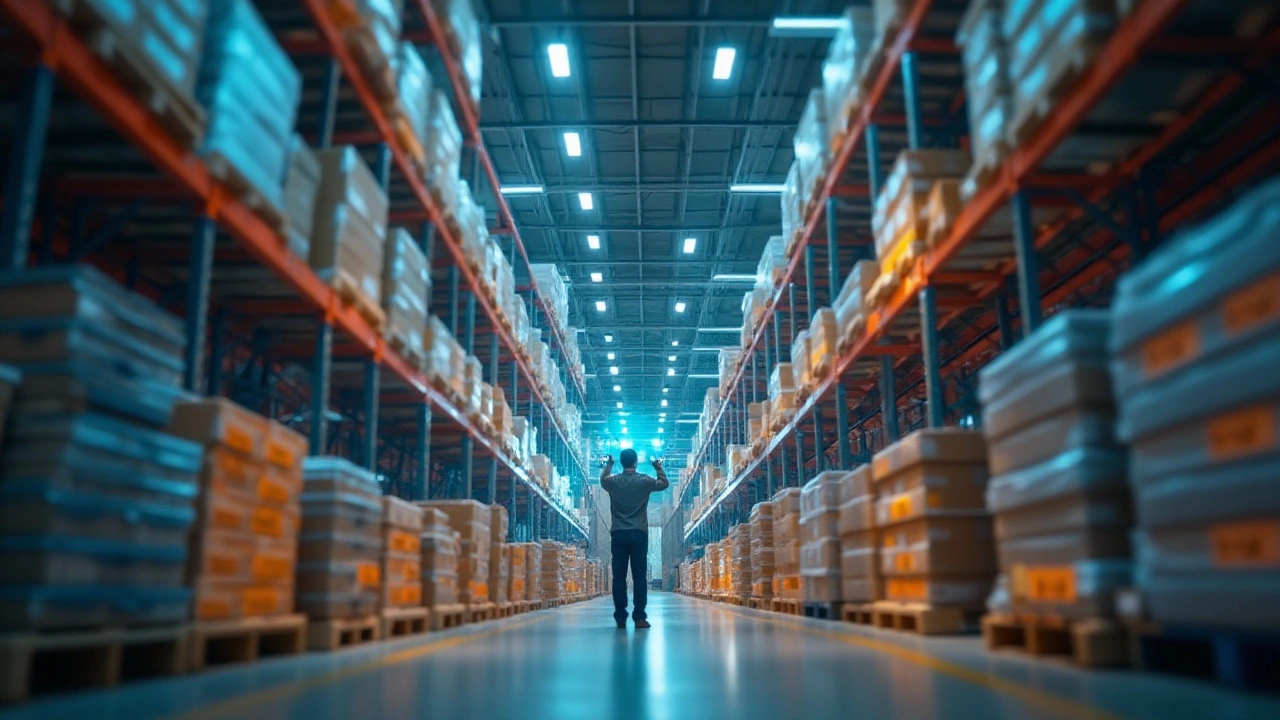
Artificial Intelligence and Machine Learning
In the realm of warehouse management, Artificial Intelligence (AI) and Machine Learning (ML) are proving to be transformative forces. These technologies have the potential to significantly enhance efficiency by predicting demand patterns, optimizing the supply chain, and even anticipating equipment maintenance needs before they arise. Imagine a warehouse system that not only comprehends the current inventory levels but also predicts what stock is likely to run low during particular seasons or promotions. This predictive capability is what AI and ML bring to the table, allowing businesses to prevent stockouts and overstock scenarios, which are common headaches for many managers.
AI algorithms learn from historical data, making them incredibly adept at pattern recognition. This is especially beneficial in devising strategies for inventory replenishment, helping warehouses strike a balance between having too much or too little stock. A prominent feature of AI systems is their ability to get smarter over time; the more data they process, the better they become at making accurate forecasts. In a 2023 report by the International Federation of Robotics, it was forecasted that AI-driven automation could lead to a 30% increase in warehouse efficiency in the coming years.
"The integration of AI in warehouse operations is not just a trend; it's a necessity for meeting the fast-paced demands of today's market," said John Smith, a logistics analyst at Gartner.
In addition to inventory management, AI is playing a crucial role in enhancing customer satisfaction by ensuring faster and more accurate order fulfillment. It can also optimize routes within the warehouse for pickers, reducing the time and fuel spent on retrieving items. By analyzing data, AI systems recommend the best paths for forklifts and other machinery, enabling seamless operations even during peak hours. Furthermore, ML models have shown a capacity for identifying potential delays in the supply chain. By recognizing patterns and anomalies in supply shipments, these models alert managers ahead of time, allowing them to take preventive measures.
The security aspect of AI is another area that's gaining traction. With sophisticated algorithms, warehouses can enhance their security measures by monitoring for unauthorized access and anomalies in real-time. These systems are not limited to physical security but also encompass network security, ensuring that all technological systems within the warehouse are safeguarded against cyber threats. In a case study by McKinsey, a warehouse that implemented AI-driven security solutions reported a 50% reduction in security breaches over a six-month period. This showcases the potential of AI as a comprehensive solution beyond just logistics and inventory management.
Automation facilitated by AI and ML doesn't just mean replacing human workers with robots, but a synergy where technology assists human efforts for a more efficient workflow. Workers can focus on complex tasks that require human intervention while leaving repetitive and monotonous jobs to machines. This balance can lead to enhanced job satisfaction and productivity. According to the Bureau of Labor Statistics, jobs in the logistics and warehousing industry are expected to grow by 7% by the end of the decade, partly due to the new roles created by AI technology. In summary, while the introduction of AI might seem daunting, the benefits it offers to the warehousing sector are extensive and undeniably valuable.
The Internet of Things (IoT) in Inventory Management
In today's rapidly advancing world, the Internet of Things (IoT) is emerging as a powerful ally in the field of inventory management. Imagine a network where machines, devices, and systems communicate together seamlessly, reducing human error and increasing efficiency. IoT enables this by linking various warehouse assets, from shelves and pallets to forklifts and conveyer belts, creating a richly interconnected ecosystem. This ecosystem helps in achieving real-time data collection and analysis, allowing companies to make informed decisions regarding their inventory.
With IoT, data is gathered from sensors placed throughout a warehouse. These sensors track inventory levels, monitor environmental conditions, and even observe equipment status. For instance, temperature-sensitive goods, like pharmaceuticals or fresh produce, can benefit immensely from IoT's capability to monitor temperature fluctuations. A slight increase or decrease can trigger alerts allowing personnel to take corrective action immediately, thus preventing costly spoilage. This proactive approach boosts not only the health of inventory but also the health of the balance sheet.
The integration of IoT into warehouse management has also streamlined the replenishment process. With automated systems in place, inventory levels trigger reorders automatically when they fall below a threshold, ensuring that stocks are consistently maintained, mitigating any risk of overstocking or stockouts. Additionally, the transparency provided by real-time data means that workers are always aware of the exact location of each item in the warehouse. This transparency greatly reduces the time wasted searching for misplaced items, thus enhancing the overall efficiency of operations.
Real-World Impact of IoT
An excellent example of IoT's effectiveness can be seen in large-scale warehouses operated by industry giants. One such company integrated IoT sensors, leading to a 25% reduction in operational costs within the first year of implementation. This was corroborated by a study published by the Logistics Bureau, claiming that businesses implementing IoT in their warehouses can expect a 20-50% reduction in inventory carrying costs.
“By modernizing warehouse practices with IoT, companies not only improve efficiency but also gain a competitive edge when meeting consumer demands,” notes a report from Gartner.
Adopting IoT technology does require an initial investment, but the return on investment is quickly apparent. The visibility and control that IoT technology provides lead to reduced handling times, minimized unused stock, and faster order fulfillment. It also spares human workers from routine tasks, allowing them to focus on more complex responsibilities. As IoT continues to evolve, its potential applications in inventory management will likely become more sophisticated, offering even more innovative solutions to age-old logistical challenges.
The adoption of the Internet of Things in inventory management is revolutionizing the industry. By enabling precise tracking and monitoring, it empowers businesses to be more agile and customer-centric. As the world moves towards digital interconnectedness, staying ahead of the curve with IoT is not just beneficial—it's essential for success in the modern warehousing landscape.
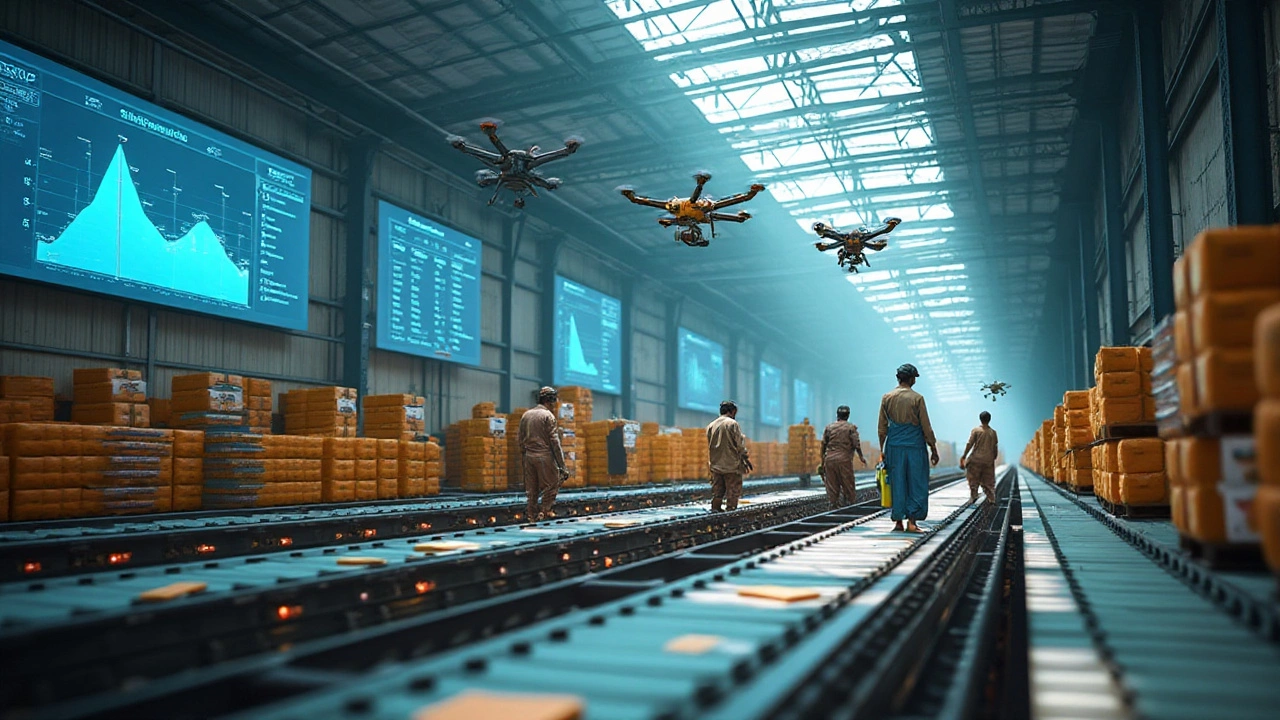
Robotics Enhancing Storage and Retrieval
In recent years, the adoption of robotics in warehouses has gained significant momentum, revolutionizing the way storage and retrieval processes are carried out. These robots are capable of performing tasks with incredible precision and efficiency, far surpassing human capabilities in certain areas. One of the most remarkable aspects of warehouse robotics is their ability to optimize space utilization, making it possible for businesses to store more products in smaller areas. This is achieved by using advanced automation technologies, where robots can navigate complex inventory environments, reaching shelves and retrieving items with minimal supervision.
These innovations are not just about cutting down human labor; they're about enhancing the entire supply chain process. For instance, with the integration of robotics, picking and packaging times can be significantly reduced, allowing for faster order fulfillment and increased customer satisfaction. Amazon, a leader in the use of warehouse technology, employs a fleet of Kiva robots that handle storage and retrieval. These robots seamlessly glide across the warehouse floor, guided by a sophisticated system that prevents collisions and ensures smooth operations. This level of automation not only speeds up processes but also minimizes errors, leading to fewer instances of incorrect orders being dispatched.
"The future of manufacturing includes robots, but to be successful, you need to have humans accompanying the robots," suggests Rodney Brooks, a robotics pioneer, highlighting the importance of human-robot collaboration.When considering the implementation of robotics in warehouse management, potential concerns often revolve around job displacement. However, the reality is robots and humans can function in synergy. Robotics are used to perform repetitive and physically taxing tasks, thus freeing up human workers to focus on more strategic and decision-oriented roles. This shift in roles often results in job enrichment and a safer work environment, as dangerous tasks are delegated to machines that are built to handle them without risk.
One noteworthy trend in the evolution of warehouse robotics is the increased usage of autonomous mobile robots (AMRs), which differ from automated guided vehicles (AGVs) by their ability to navigate without external guidance, allowing for more flexible operations. AMRs often use sensors and onboard computers to map their environment and determine the most efficient paths through the warehouse. This dynamic navigation capability allows them to avoid obstacles and find alternative routes, ensuring that operations continue smoothly even in bustling environments. This adaptability is particularly beneficial during peak seasons when warehouses face heightened activity levels.
As the technology continues to mature, we are witnessing interesting applications such as collaborative robots, or cobots, which are designed to work alongside humans. Cobots are often equipped with intuitive interfaces and safety features that enable them to operate safely near their human counterparts. This includes sensors that detect human presence and automatically slow down or stop movements to avoid accidents, thus creating a more harmonious and productive workspace. The adoption of such technologies is not only about introducing efficiency but also about reshaping the workforce in a way that leverages both human creativity and robotic precision.
Year | Robotics Market Value (USD Billion) |
---|---|
2020 | 13.6 |
2022 | 17.5 |
2024 | 21.0 |
The supply chain benefits from robotics go beyond current gains; future innovations are likely to expand upon the capabilities already in place. With advances in artificial intelligence and machine learning, robots are expected to become even more autonomous, capable of learning from past data to make predictive decisions about supply chain logistics. The potential savings in time and cost are enormous, making warehouse robotics a compelling investment for modern businesses aiming to remain competitive in a rapidly evolving market.
Future Trends and Innovations
As we peer into the future of warehouse management, it's clear that technology will continue to propel the industry into new territories. The relentless pace of change is setting the stage for innovations that will further enhance efficiency, accuracy, and flexibility. One major trend that's gaining traction is the adoption of predictive analytics. By leveraging vast amounts of data collected through IoT devices and automated systems, warehouses can forecast demand with remarkable precision. This not only helps in optimizing stock levels but also in minimizing wastage, ensuring the right products are available when they are needed the most.
Meanwhile, the role of artificial intelligence in warehouse environments is expanding beyond its current applications. Future systems may be able to autonomously learn from their environments and continuously improve their processes without human intervention. This self-optimization can dramatically reduce costs and increase output, allowing businesses to remain competitive in a demanding market. Additionally, these AI-enabled systems could play a crucial role in enhancing safety protocols by predicting potential risks and suggesting proactive measures, thereby safeguarding human workers from unforeseen hazards.
Robotics is another area poised for revolutionary advancements. The next generation of warehouse robots will likely exhibit greater dexterity and cognitive functionalities. This means they'll be able to handle an even more diverse array of tasks, from sorting fragile items to assembling complex orders. Collaborative robots, or cobots, are expected to work alongside humans, complementing their strengths and creating a symbiotic work environment. According to a recent study by the International Federation of Robotics, the installation of industrial robots has surged by 10% to prioritize efficiency and precision in industrial and warehouse settings.
The Rise of Green Technologies
There's a growing emphasis on sustainable practices within supply chain management, and warehouses are no exception. Efforts to reduce environmental footprints are driving the adoption of eco-friendly technologies and processes. For instance, smart energy management systems are just one element of creating more sustainable operations, which can help reduce energy consumption and operational costs by monitoring and optimizing the use of power across facilities. Warehouses may also begin integrating renewable energy sources, such as solar panels, into their infrastructure, further decreasing their reliance on traditional power grids and contributing to a greener planet.
"The integration of sustainability into supply chain operations is no longer optional. It is a critical imperative to not only achieve regulatory compliance but also meet market demands for environmentally conscious business practices," said a report from the World Economic Forum.
Moreover, the advent of biodegradable packaging materials is set to transform the way products are packed and shipped. By choosing these materials, warehouses can minimize their contribution to landfill waste while complying with increasingly stringent environmental regulations. As sustainability continues to be a key consideration for businesses, future warehouses may also strive towards achieving carbon-neutral operations through a combination of smart technology and innovative practices.
Write a comment