When it comes to massive warehouse operations, one name stands above the rest: the biggest warehouse company in the world. But what makes it so enormous? Well, it’s not just about size; it’s about reach, technology, and efficiency. This global giant operates thousands of facilities across continents, ensuring the smooth flow of products from manufacturers to your doorstep. That's pretty impressive, right?
So, how does this colossal company manage to keep everything running smoothly? One word: automation. By integrating cutting-edge technology into their processes, they’ve revolutionized how warehouses function today. From robotic picking systems to AI-driven inventory management, they’re a step ahead in optimizing operations.
- Introduction to the Giant
- Global Reach and Scale
- Innovative Practices
- Technology and Automation
- Customer Service Excellence
- Future of Warehousing
Introduction to the Giant
So, who holds the crown in the warehouse solutions world? It’s none other than Amazon. This powerhouse of logistics isn’t just the biggest in terms of size; it’s also a leader in innovation and reach. Their network of warehouses, often called fulfillment centers, spans across the globe, strategically positioned near major markets to ensure quick delivery times.
Founded by Jeff Bezos in 1994, what started as an online bookstore quickly expanded into a global e-commerce titan. By continually expanding its logistics footprint, Amazon now boasts over 175 fulfillment centers worldwide, covering millions of square feet. Talk about massive scale!
Global Reach and Scale
Amazon's facilities are located in over 20 countries, including the United States, Germany, Japan, and India, among others. This massive network allows them to deliver to customers at lightning speed, often within a day or two. Here's a snapshot of their warehouse presence by regions:
Region | Number of Facilities | Square Footage (approx.) |
---|---|---|
North America | 100+ | 100 million+ |
Europe | 45+ | 40 million+ |
Asia-Pacific | 30+ | 30 million+ |
With such a sprawling network, no surprise Amazon leads the chart of the largest warehouse company globally.
Why Size Matters
Being the largest comes with its perks. For Amazon, it means enhanced economies of scale. This sheer size reduces per unit costs, allowing for free shipping offerings that keep us all coming back for more. Additionally, their integration of logistics and technology ensures better inventory management and delivery accuracy.
But size is just one part of their secret sauce. Next, we'll explore how technology and automation play a crucial role in maintaining their lead.
Global Reach and Scale
When we talk about the biggest warehouse company, we're not just yapping about large square footage. We're diving into a global network that connects countries, oceans, and people. The scale of its operations is nothing short of jaw-dropping.
This company operates an immense network that spans over hundreds of facilities in more than 60 countries. That means they can move products pretty much everywhere. Need goods delivered from Tokyo to Toronto? They've got that covered.
Thanks to their strategic placement of warehouses near major shipping ports and urban centers, they cut down transportation times significantly. It's all about efficiency, folks!
Steps to Global Operations
- Identify crucial markets worldwide: This involves analyzing which areas have high demand and would benefit from a nearby distribution center.
- Strategic placements: Setting up warehouses near shipping ports or in bustling urban locations ensures timely deliveries and cuts transport costs.
- Local partnerships: Collaborating with local logistics companies helps navigate various regional regulations and infrastructures, ensuring smoother operations.
According to recent stats, this powerhouse processes over 100 million shipments annually. That's a lot of boxes whizzing around the world!
Region | Number of Warehouses |
---|---|
North America | 250+ |
Europe | 300+ |
Asia | 200+ |
Other Regions | 150+ |
What makes this even more incredible is their ability to adapt to market changes swiftly. A sudden spike in demand? They optimize routes, shift resources, and tackle the challenge. So, the next time you're waiting eagerly for your package, think about the intricate dance happening behind the scenes!
Innovative Practices
Delving into the innovative side, the largest warehouse company in the world continuously adapts and thrives by leveraging cutting-edge strategies. One of their game-changers is the use of robotic automation. By deploying robots for tasks like picking, packing, and sorting, they skyrocket efficiency and accuracy. Think of it as having an extra set of incredibly fast hands.
Additionally, they've embraced AI for optimizing routes, minimizing delivery times, and cutting costs. This ensures that customers receive their packages faster and with minimal error. Who doesn’t love a speedy delivery?
Harnessing Green Initiatives
It's not just about speed; sustainability is top of mind, too. By integrating energy-efficient practices, like solar panels and electric forklifts, they’ve reduced their environmental footprint. A move towards green logistics shows their commitment to a sustainable future.
"Our mission is to innovate in a way that serves both our customers and the planet," says the company’s sustainable practices lead.
Emphasizing Smart Warehousing
They also make use of smart warehousing, a term that involves IoT sensors and real-time data analytics. These technologies help monitor inventory levels, track products, and forecast demand accurately. By having a clear picture of what’s in stock and what's trending, they can adjust strategies on the fly.
Leading Through Tech
In the competitive warehouse solutions market, staying ahead requires constant evolution. By integrating these innovative methods, they set themselves apart from the rest. Their commitment to pioneering new technologies doesn’t just streamline their own operations but often sets industry standards others strive to imitate.
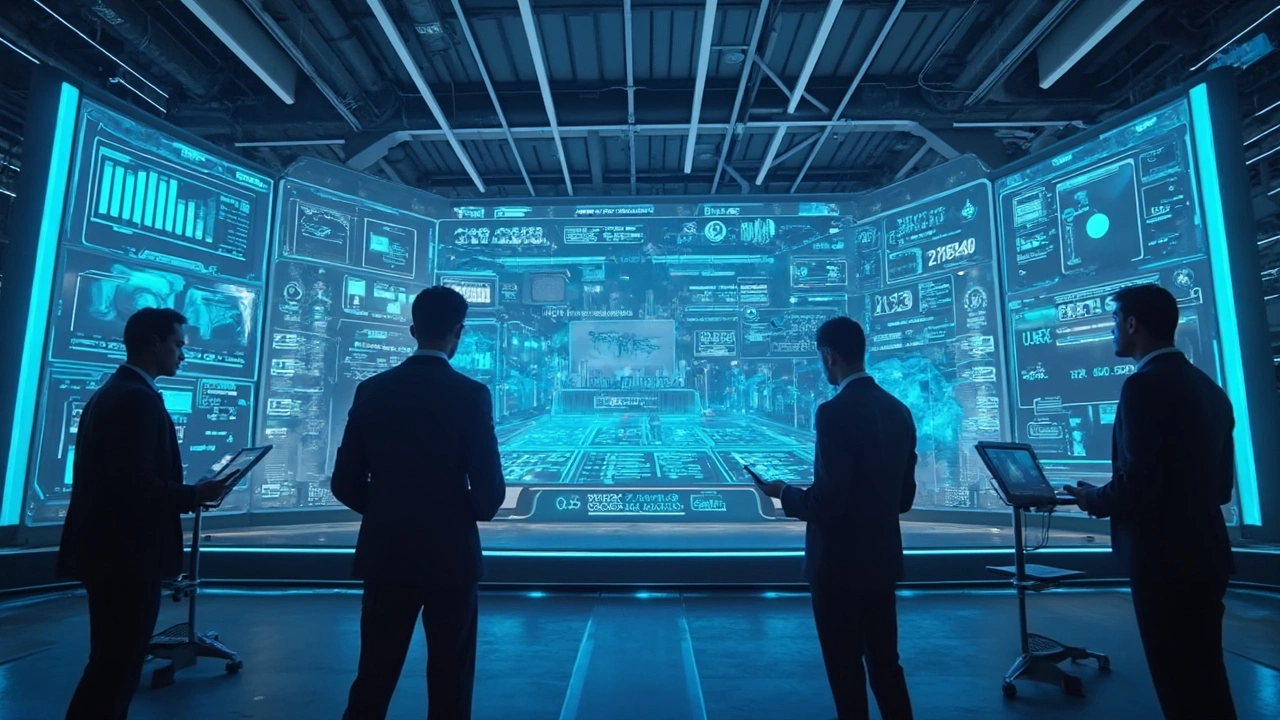
Technology and Automation
The biggest warehouse company in the world has transformed its operations with cutting-edge technology and automation. Their facilities are teeming with robots and smart systems, which are game-changers in managing logistics efficiently.
One of the key technologies they use is automated guided vehicles (AGVs). These aren't your typical forklifts—AGVs navigate the warehouse floors with precision, carrying loads from one point to another, reducing errors and speeding up operations significantly. It's like having a team of silent, tireless workers zipping around 24/7.
Robotics in Action
Robots are not just for sci-fi movies. In a modern warehouse, robotic arms pick items from shelves with incredible accuracy and speed. This automation ensures faster order fulfillment and minimal human error.
Imagine a robotic arm picking your order in a matter of seconds—that's the level of efficiency we're talking about. Plus, employees' roles have evolved from manual workers to tech-savvy operators who manage these high-tech devices, enriching the workforce skill set.
Data-Driven Decisions
Data is the backbone of their operations. By collecting real-time data at each stage of the supply chain, they can eliminate bottlenecks and optimize their processes. Predictive analytics help them anticipate demand shifts and stock important items before they even become a trend—how's that for being proactive?
Technology | Efficiency Gain |
---|---|
AGVs | 30% faster material handling |
Robotic Picking | 50% reduction in order picking errors |
Data Analytics | 25% improvement in demand forecasting |
With these innovations, the company sets benchmarks in the warehouse solutions industry. They've not only boosted operational efficiency but also drastically improved customer satisfaction, keeping them at the top of their game.
Customer Service Excellence
In the world of warehousing, keeping customers happy is crucial. The biggest warehouse company excels in customer service by maintaining transparency and reliability in their operations. They know that ensuring fast and accurate deliveries is a key part of building trust with clients.
One big win for them is their robust tracking system. Customers love knowing exactly where their shipments are at any point. This company offers real-time tracking updates, reducing anxiety over lost or delayed packages. It's all about making things stress-free!
They also prioritize feedback. After a delivery, they actively collect customer opinions through surveys and direct communication, churning these insights into improving their services. It's a classic example of listening to your audience—it works wonders when done right.
Focus on Personalization
They’ve taken steps beyond just standard service. By harnessing data analytics, they tailor solutions to meet individual client needs. This means customized solutions for both the largest corporations and the smallest online sellers.
- Tailored logistics planning to fit different business models.
- Flexible shipping options across different channels.
- Custom packaging and labeling to match branding requirements.
Personalization enhances client relationships, leading to loyalty and repeated business.
Response Time and Issue Resolution
This warehouse giant emphasizes quick response times to any issues. They have dedicated support teams ready to resolve problems efficiently. Whether it's a shipment delay or a billing question, they aim to turn around responses fast, ensuring no customer feels left hanging.
An internal study showed that swift issue resolution increased their client retention rate by 20%. It's clear that reliable service is not just a nice-to-have, but a business necessity.
All these efforts showcase why they lead in not just size, but in fostering customer service excellence too. It's a mix of technology, personalization, and good old-fashioned listening that sets them apart.
Future of Warehousing
The future of warehousing is looking incredibly high-tech. As companies scramble to meet increasing global demand, the role of advanced technology will be more critical than ever. Imagine a warehouse where shelves restock themselves or a system that predicts customer needs before inventory runs low—that's where we're headed.
Automation and Robotics
Automation isn't just a buzzword; it's the backbone of tomorrow's warehouse solutions. Robotics will play a major role, taking over repetitive tasks and helping businesses scale bigger. Companies are already using automated guided vehicles (AGVs) and drones for inventory checks, reducing human error and speeding up operations.
AI and Machine Learning
Artificial Intelligence (AI) is set to further revolutionize how warehouses manage tasks. With machine learning algorithms, companies can predict trends, adjust inventory in real time, and optimize delivery routes. This proactive approach not only streamlines the process but also leads to significant cost savings.
Sustainable Practices
The future of warehouse operations isn't just tech-focused; it's green too. As industries push for sustainability, warehouses will employ energy-efficient practices—from solar panels to green logistics. Environmentally-friendly packaging and waste reduction methods will also become essential components.
According to recent studies, implementing sustainable practices can reduce operational costs by 20% over five years. Check out the data:
Years Implemented | Cost Reduction (%) |
---|---|
1 | 5% |
3 | 12% |
5 | 20% |
Adapting to these changes means that the largest warehouse company and its competitors will continue innovating to stay ahead of the pack. Whether you’re interested in global Shipping trends or aspiring to use warehouse solutions in your own business, staying updated on these advancements is key.
Write a comment