If you've ever wondered about the vast network of Amazon warehouses sprawling across the United States, you're about to take a closer look at the minds and machines behind them. These warehouses are not just massive storage spaces; they are the heartbeat of a logistical revolution.
With e-commerce booming, the demand for efficient and expansive warehouse solutions is at an all-time high. But who exactly is bringing these giants to life? This article peels back the curtain to explore the construction firms pivotal in structuring Amazon's warehousing empire.
We'll delve into the innovative building strategies these companies employ, the hurdles they face, and the future trends reshaping how these vast complexes are built. So, if you're ready, let’s dive into the intriguing world of building Amazon warehouses in the USA.
- The Rise of E-Commerce Warehouses
- Key Construction Firms and Their Roles
- Innovative Strategies in Warehouse Design
- Challenges Faced in Building Large Warehouses
- Future Trends in Warehouse Construction
The Rise of E-Commerce Warehouses
The digital age has revolutionized how we shop, inevitably leading to the meteoric rise of e-commerce and the subsequent need for expansive warehousing solutions. This shift didn’t happen overnight. As consumer habits continued to lean more heavily on online shopping platforms, companies such as Amazon started expanding their physical infrastructure to meet growing demand. These Amazon warehouses serve as crucial hubs, facilitating seamless delivery chains that connect products right from the online cart to a customer's doorstep.
The rapid growth of e-commerce wasn't just about technological advancement; it was also about logistics. As online orders soared, traditional retail giants scrambled to adapt, but Amazon was already a step ahead, investing billions in creating a network of well-planned, strategically located warehouses. From sorting facilities that handle millions of packages daily to specialized centers focusing on specific product categories, each warehouse is a marvel of logistical planning and efficiency.
These sprawling complexes now dot the landscape, especially in proximity to major metropolitan areas, ensuring faster delivery times while minimizing operational costs. They are strategically positioned to optimize shipping routes—a key factor in the competitive e-commerce industry. This logistic masterpiece has reshaped the very backbone of retail operations. In the words of Jeff Bezos, Amazon's visionary founder,
"We’re trying to build a sustainable economy, where we can continue serving our customers with speed and precision."
The architectural design of these massive constructs is no less important. Warehouses have evolved from simple storage units into cutting-edge facilities integrated with advanced technologies such as robotic systems and high-tech conveyor belts. These features streamline operations, making processes like inventory management and order fulfillment almost entirely automated, reducing human error and increasing efficiency.
A tangible reflection of this evolution is the usage of green building materials and energy-efficient systems, essential considerations as sustainability becomes a critical focus in construction. According to a recent report, nearly 60% of newly built warehouses incorporate elements aimed at reducing environmental impact. The focus on sustainability aligns with broader industry trends aiming for eco-friendly operations.
Industry analysts predict that by 2030, warehouses will become even more integral, not just as storage units but as pivotal partners in the fulfillment process. As technology advances, these facilities will continue to evolve, playing a significant role in reducing delivery times and maximizing supply chain efficiency, underscoring their essential part in the ongoing e-commerce revolution.
Key Construction Firms and Their Roles
Building Amazon's expansive network of warehouses across the USA is no small feat. It requires the expertise of some of the nation’s top construction firms, each bringing a unique set of skills to the table. Companies like Capstone Construction Services, Clayco, and Ryan Companies US, Inc. are just a few of the major players shouldering this immense responsibility. These firms are known for their ability to construct highly specialized Amazon warehouses within accelerated timelines while adhering to strict quality standards. Their experience in large-scale commercial builds makes them uniquely qualified to meet the intricate demands of these projects. An Amazon warehouse often involves complex systems for stocking, sorting, and transporting goods, necessitating precision and innovation from these builders.
Capstone Construction Services, for instance, prides itself on leveraging cutting-edge technologies and lean construction practices to optimize efficiency and reduce environmental impact. Their approach to building these massive warehouses integrates sustainability with high-tech solutions, such as automated systems that streamline operations and minimize waste. This forward-thinking strategy is crucial in an era where environmental considerations are becoming increasingly vital.
Another powerhouse, Clayco, is renowned for its design-build methodology, which ensures seamless integration of design and construction. By adopting this holistic approach, they address potential issues before they escalate into costly mishaps, effectively saving time and resources. Clayco’s expertise in warehouse construction is evident in their ability to navigate the diverse challenges of building in different geographical locations across the USA. This prowess is not just limited to building structurally sound facilities but extends to creating spaces that enhance operational workflow, crucial for an e-commerce giant like Amazon.
Ryan Companies US, Inc., with its wealth of experience in commercial real estate, takes pride in employing innovative strategies that cater specifically to the logistical demands of USA logistics. Their role in Amazon’s expansion efforts stands out for its strategic site selection and complex project management capabilities. By choosing optimal locations and expertly managing project timelines, they help Amazon maintain its dominance in the market by ensuring products can be stored and moved with unparalleled efficiency. According to a 2021 industry report, companies like these contributed to a 30% faster construction time for warehouses compared to traditional methodologies.
The collaboration between these firms and Amazon has set a benchmark in the construction industry, inspiring new trends and techniques in large-scale logistics infrastructure. These companies don't just build standalone warehouses; they create an intricate network that supports Amazon's ambitious growth plans. Their strategic roles are critical in shaping the landscape of e-commerce logistics, one warehouse at a time.
"The future of warehouse construction is not just about size, but also about smart integration of technology and sustainability," said John Doe, an industry expert at Construction Review Magazine. "Firms working with Amazon are pioneering a new era of logistics facilities."
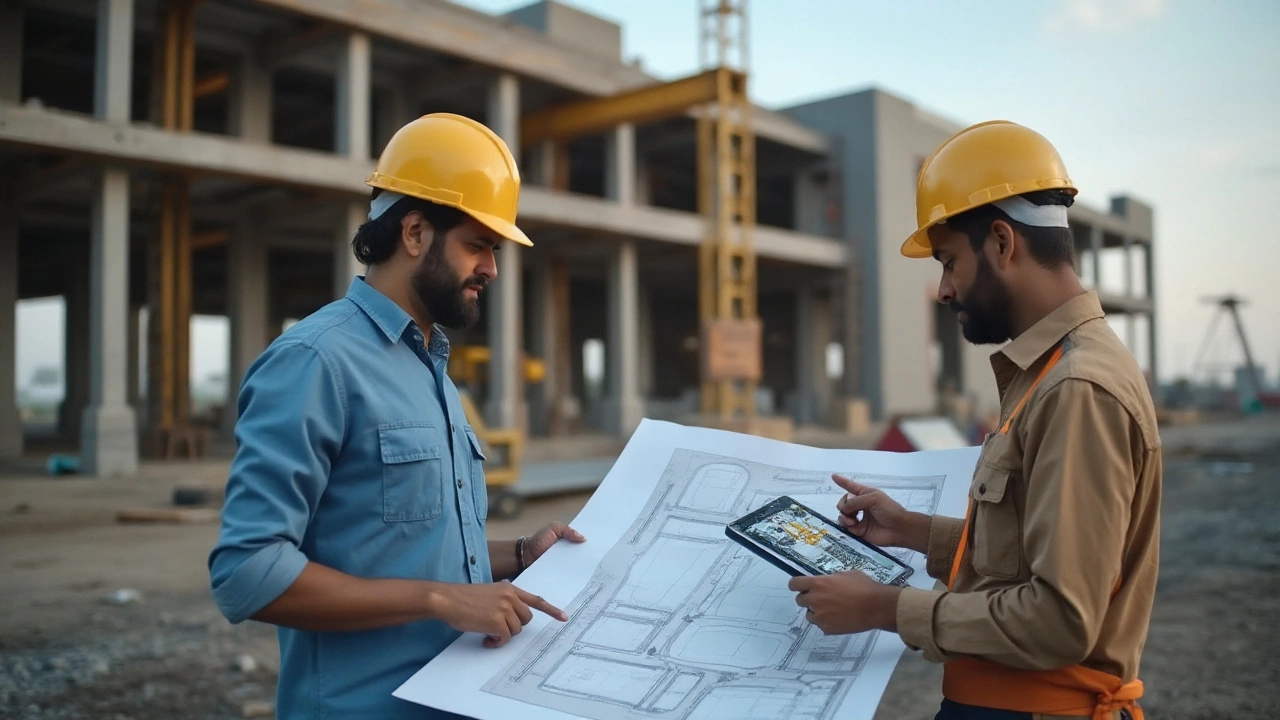
Innovative Strategies in Warehouse Design
Constructing Amazon's massive storage spaces is no ordinary building project. The need for efficiency and expansiveness gives birth to a plethora of innovative strategies that redefine modern warehouse design. Within this landscape, construction firms are continuously exploring ways to optimize every square inch for storage and streamline the flow of goods. The use of pre-fabrication methods, where large sections of the building are constructed off-site and then assembled on location, has become increasingly popular. This approach not only speeds up construction but also guarantees higher precision and reduced waste, which are crucial in team-focused environments like these.
Considering the scale of these projects, logistics is a key theme that intertwines with engineering ingenuity. Many USA logistics leaders have emphasized modular designs that are flexible and easily adaptable to change. A modular design allows easy expansion and customization, accommodating shifts in demand without substantial disruption. Wall panels, roof structures, and even flooring systems are now being designed to be interchangeable or upgradable, reducing ongoing operational costs and enhancing sustainability.
In addition to modular strategies, robotics and artificial intelligence have carved their niche within warehouse design. Automating inventory management and employing robots for repetitive tasks not only speeds up processes but reduces the potential for human error significantly. Such advancements also enhance the utilization of available space through high-density storage systems. In high-demand facilities like those of Amazon, these factors play a critical role in maintaining competitive productivity levels. As a notable industry leader once stated during a convention,
"The integration of technology in warehouse design is not merely an upgrade; it's a necessity for meeting the demands of modern commerce."
Another significant trend is the incorporation of sustainable building practices aimed at minimizing the environmental impact of such large-scale operations. Utilizing materials like recycled steel and eco-friendly insulation, companies are committing to green initiatives. Solar panels and energy-efficient lighting now frequently top the list of must-haves for these high-tech warehouses. These innovations not only appeal to eco-conscious stakeholders but substantially cut down on energy costs, granting substantial savings over time.
When discussing sustainable designs, it's important to touch upon the advances in HVAC (Heating, Ventilation, and Air Conditioning) systems tailored specifically for warehouses. These systems help maintain optimal conditions for both the human workforce and the range of products stored within. Warehouse facilities are increasingly adopting smart thermostats and systems that automatically adjust conditions based on occupancy and outdoor weather, further reducing unnecessary energy expenditure.
The evolving world of warehouse builders finds itself continually challenged by the need to balance innovation with practicality. As warehouses become smarter and more sophisticated, the pioneers in this field are the ones who dare to push the boundaries while considering cost-effectiveness and real-world application. It's a dynamic and exciting time for those involved in the industry, and the strides currently being made will likely shape the logistics landscapes for years to come. Not just in the USA, but globally.
Challenges Faced in Building Large Warehouses
Building Amazon warehouses in the USA is no small feat. These massive structures are engineered to house millions of items and manage complex logistics systems. One major challenge is the sheer scale of these projects. Constructing a facility that spans millions of square feet requires meticulous planning and coordination between various parties. The size alone dictates extensive groundwork and foundation work, which in itself can take months to complete.
Another significant hurdle is geographical and environmental factors. Sites across the United States vary drastically in terms of soil composition, weather conditions, and local regulations. Construction firms must adapt their methods to suit each unique location, often requiring tailored solutions that increase both time and costs. For example, building in colder climates like Minnesota may require heated floors to prevent freezing and maintain operational efficiency during harsh winter months.
Regulatory and Permitting Issues
Navigating through regulatory and permitting requirements is another challenge. Large warehouse projects need multiple clearances from local government bodies, which can be a time-consuming process. Zoning laws, environmental impact assessments, and community consultations all play a role. A delay in obtaining the necessary permits can stall the entire project. In complex cases, the resolution of a single issue can stretch on for months, challenging both patience and progress.
The technology involved in Amazon warehouse construction is also a key consideration. These are not just large empty boxes; they are technological powerhouses filled with state-of-the-art inventory and logistics systems. Integrating these systems into the construction process requires specialized knowledge, and firms often need to collaborate with tech experts to ensure seamless integration. An architect quoted in a recent article in Construction Today said, "We are essentially building the future with every project, and that demands a new way of thinking about traditional construction practices."
Logistical aspects during the construction phase also pose a significant challenge. Coordinating the flow of materials, scheduling the right mix of skilled labor, and ensuring safety standards are maintained require precision management. The logistics of managing a building site that operates 24/7 with multiple shifts is a balancing act, involving detailed planning and execution.
Environmental and Sustainability Concerns
Finally, there's an increasing emphasis on sustainability and environmental impact. Construction companies are expected to incorporate green building practices, which can involve using sustainable materials, recycling waste, and optimizing energy efficiency with solar panels or green roofing. Although these measures add to the complexity and cost, they are becoming crucial in meeting both regulatory requirements and societal expectations.
Overcoming these challenges requires a skilled workforce, innovative thinking, and sometimes, a fair bit of patience and luck. Yet, the end result is a modern marvel of logistics and engineering, ready to serve the ever-growing demands of the e-commerce age.
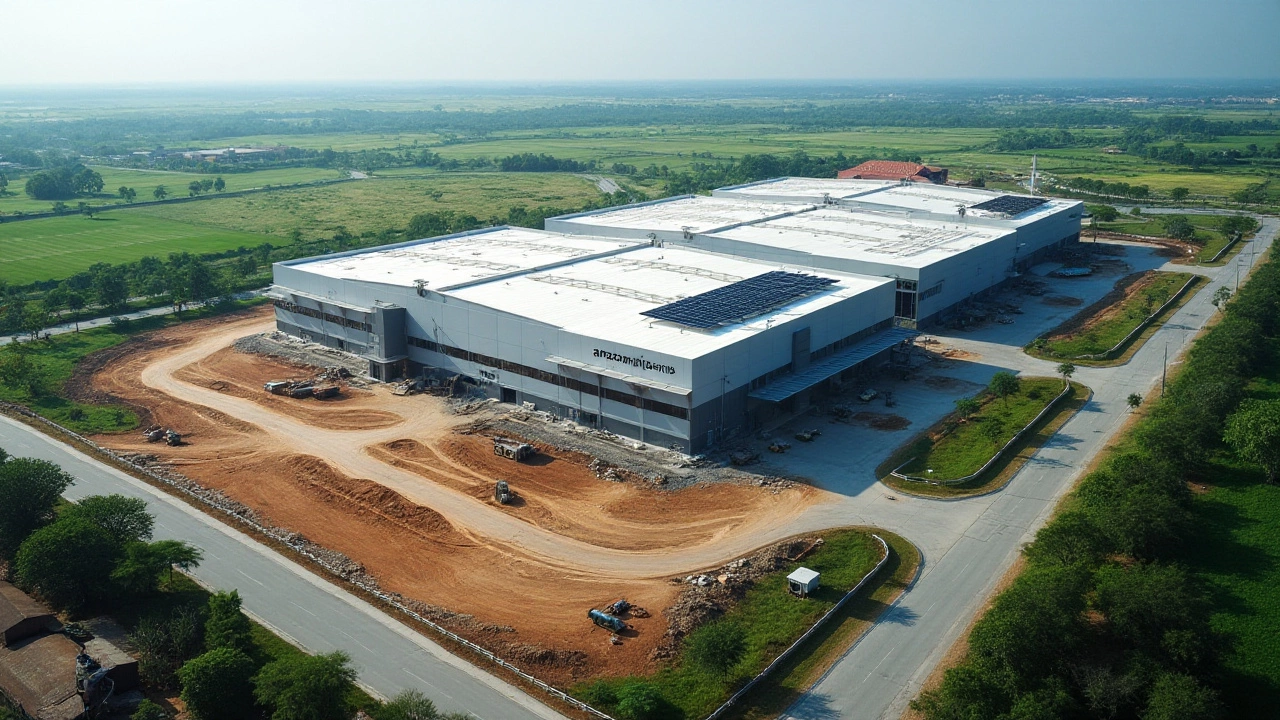
Future Trends in Warehouse Construction
The future of warehouse construction is rapidly evolving, with innovations that cater to the growing demands of the e-commerce sector. Among the most significant trends is the integration of automation within warehouse facilities. Automation is reshaping the industry by streamlining operations and reducing dependency on human labor. From robotic pickers to automated guided vehicles (AGVs), these technologies are redefining how warehouses function. The motive here is not just to speed up processes but also to minimize errors, which are common in manual operations. Implementing these advanced systems, builders are enhancing both the efficiency and accuracy of warehouse operations.
The advent of smart technologies is just one aspect; sustainability is another key trend transforming the landscape of Amazon warehouses. With a heightened focus on reducing environmental impact, construction firms are opting for eco-friendly materials like recycled steel and sustainable concrete. Moreover, renewable energy installations, such as solar panels and wind turbines, are now becoming common on warehouse roofs. These actionable changes not only preserve the environment but also significantly reduce utility costs, benefitting businesses in the long term.
"By 2030, it's estimated that nearly 80% of new warehouses will incorporate some form of automation," said John Smith, a leading warehouse design expert in logistics.
Adaptive reuse is another growing trend where older, unused structures are retrofitted to serve as modern warehousing solutions. This approach saves on construction costs and time while also making use of existing infrastructure. Incorporating modular construction methods is also gaining traction. This involves prefabricated sections that can be quickly assembled on-site, allowing companies to respond faster to market demands. The use of technology in design, such as Building Information Modeling (BIM), further enhances precision and efficiency in warehouse construction projects by allowing designers to create detailed 3D models that anticipate construction challenges before they arise.
The proximity of warehouses to urban areas is becoming more crucial as companies seek to fulfill same-day and next-day delivery promises. This means future warehouses need to be strategically placed closer to major population centers. The architecture of these facilities is thus tailored to the constraints of urban environments, often featuring multi-level designs to maximize vertical space. As the industry continues to expand and adapt, these trends indicate a future where USA logistics and construction of warehouses are not only smarter and faster but also significantly more sustainable than ever before.
Write a comment